Lean Process Optimizer - Process Streamlining Tool

Welcome! Let's optimize your processes for maximum efficiency.
Optimize workflows with AI-powered insights.
Can you help me streamline my business process by...
What are the best strategies for optimizing workflow in...
How can I identify automation opportunities in my...
I'm looking to simplify my company's process map. What steps should I take to...
Get Embed Code
Lean Process Optimizer Overview
Lean Process Optimizer is designed as a specialized tool aimed at streamlining and enhancing efficiency within various operational processes. Its core functionality revolves around identifying bottlenecks, reducing waste, and suggesting automation opportunities to improve workflow and productivity. This tool integrates principles from Lean Management and Process Optimization methodologies to deliver a tailored experience for improving business operations. For example, in a manufacturing context, Lean Process Optimizer could analyze the assembly line process to identify steps that do not add value to the end product and suggest modifications or eliminations of these steps. In a service-oriented scenario, it might evaluate customer service workflows to reduce wait times and improve customer satisfaction through process re-engineering and automation of repetitive tasks. Powered by ChatGPT-4o。
Core Functions of Lean Process Optimizer
Process Mapping
Example
Automatically creating visual representations of a company's workflows.
Scenario
For a retail company struggling with inventory management, Lean Process Optimizer could map out the entire inventory process from supplier to sales floor, highlighting inefficiencies like overstocking or understocking and suggesting just-in-time inventory practices.
Bottleneck Identification
Example
Identifying stages in a process that cause delays or inefficiencies.
Scenario
In a software development firm, it might pinpoint stages in the development cycle where projects tend to stall, such as at the testing phase, and recommend solutions to streamline testing processes.
Automation Opportunities
Example
Identifying tasks that can be automated to save time and reduce errors.
Scenario
For an accounting firm, Lean Process Optimizer could suggest automating repetitive tasks like data entry or invoice processing, freeing up staff to focus on more complex, value-added activities.
Waste Reduction
Example
Suggesting ways to eliminate unnecessary steps, resources, or time in a process.
Scenario
In a hospital's patient admission process, it might find that multiple forms collect the same information, and suggest consolidating these forms to speed up the admission process and improve patient experience.
Who Benefits from Lean Process Optimizer
Small to Medium Enterprises (SMEs)
SMEs often operate with limited resources and can significantly benefit from optimizing their processes to improve efficiency and reduce costs. Lean Process Optimizer can help these businesses identify quick wins and long-term improvements to stay competitive.
Large Corporations
Large corporations with complex processes across various departments can use Lean Process Optimizer to streamline operations, enhance cross-departmental collaboration, and leverage automation for scalability and efficiency.
Startups
Startups looking to establish efficient processes from the beginning can use Lean Process Optimizer to design lean, scalable workflows that support rapid growth and adapt to changing business needs.
Healthcare Providers
Healthcare providers can use Lean Process Optimizer to streamline patient care processes, reduce waiting times, and improve the overall quality of care by identifying inefficiencies in patient flow, staffing, and resource allocation.
Using Lean Process Optimizer: A Step-by-Step Guide
Start your journey
Begin by visiting [yeschat.ai](https://yeschat.ai) for a free trial, accessible without the need for login or a ChatGPT Plus subscription.
Identify your process
Determine the specific process or workflow you wish to optimize. Common use cases include manufacturing workflows, service delivery processes, and administrative procedures.
Map your process
Use Lean Process Optimizer to map out your current process. This involves detailing each step, decision point, and outcome within the process.
Analyze for improvement
Leverage the tool's analytics capabilities to identify bottlenecks, redundancies, and non-value-adding activities within your process.
Implement and automate
Apply the recommendations provided by Lean Process Optimizer to streamline your process. Explore automation opportunities for repetitive tasks.
Try other advanced and practical GPTs
California Drivers Handbook
Empowering safe and informed driving
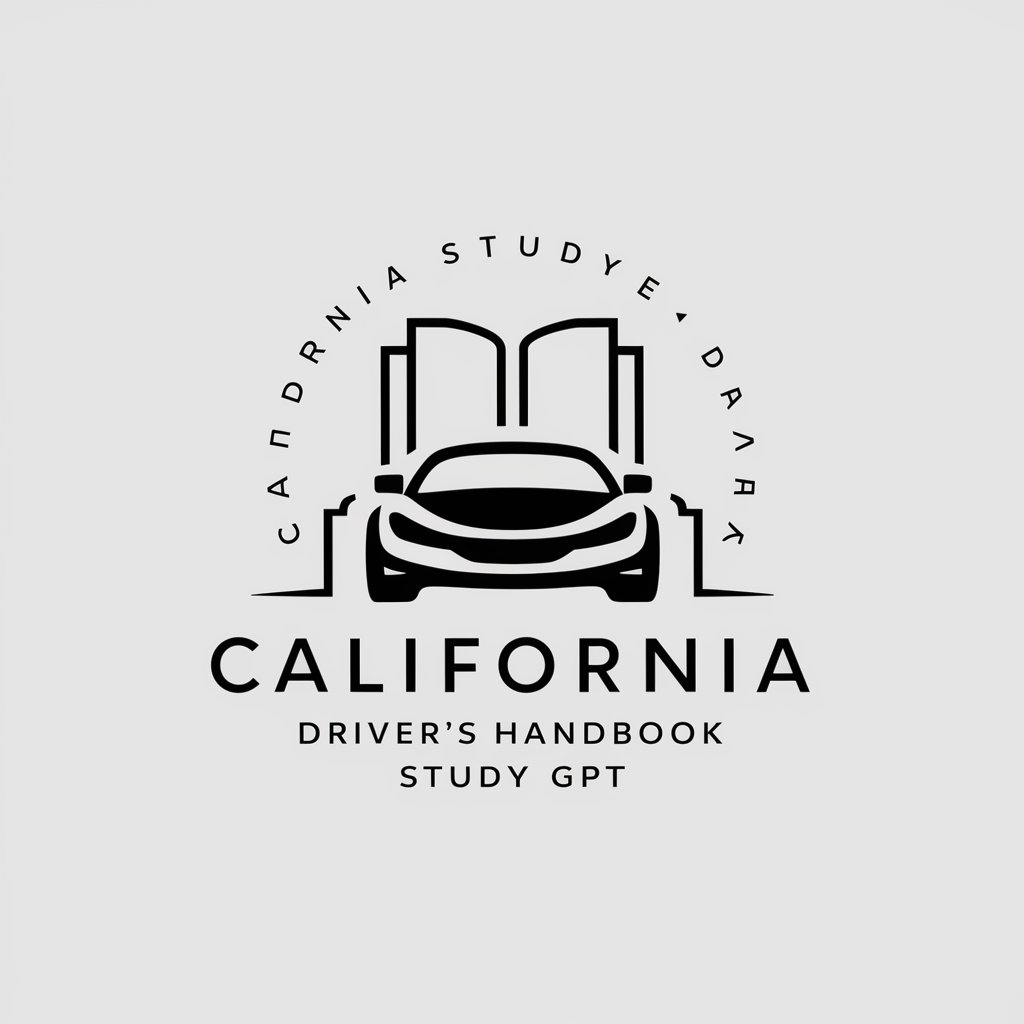
AWS Promodoc
Elevating Promotions with AI Power
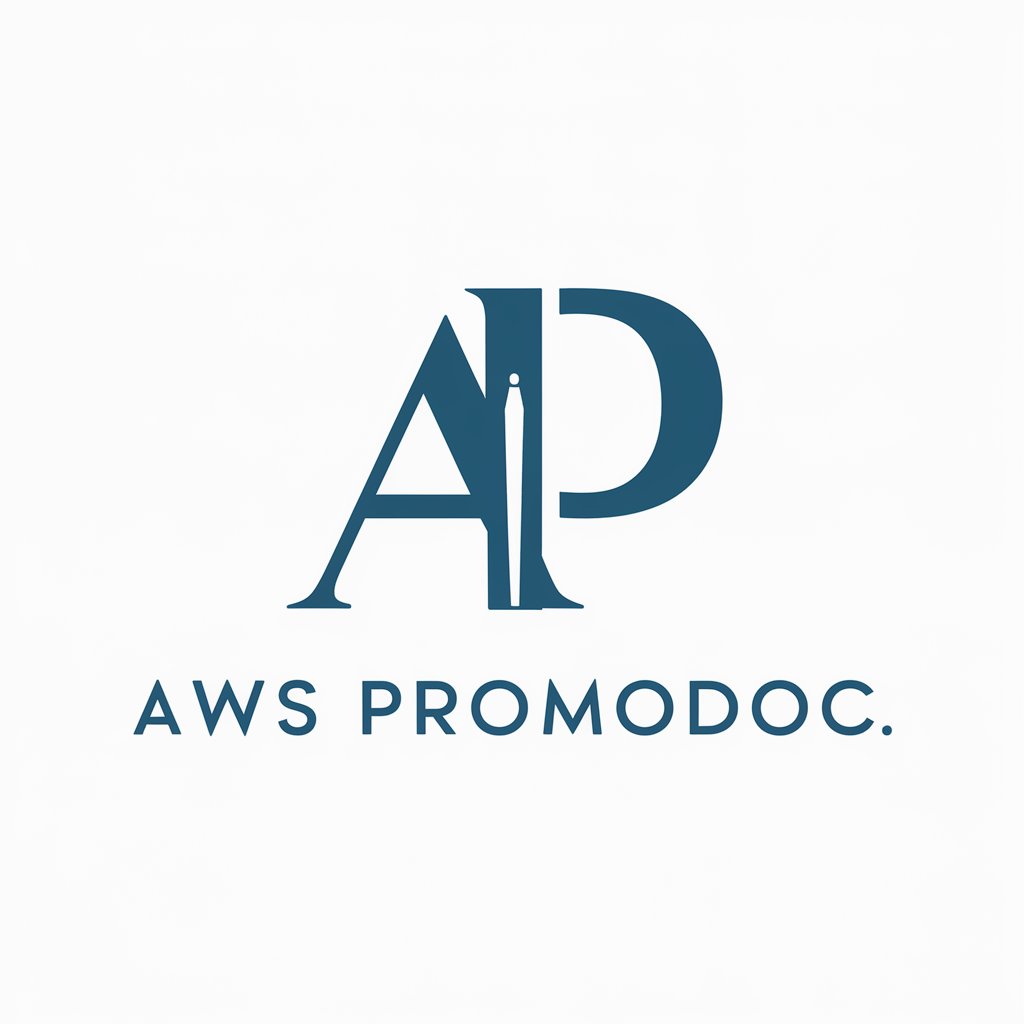
Extract keyword from aricle
Uncover Key Insights with AI
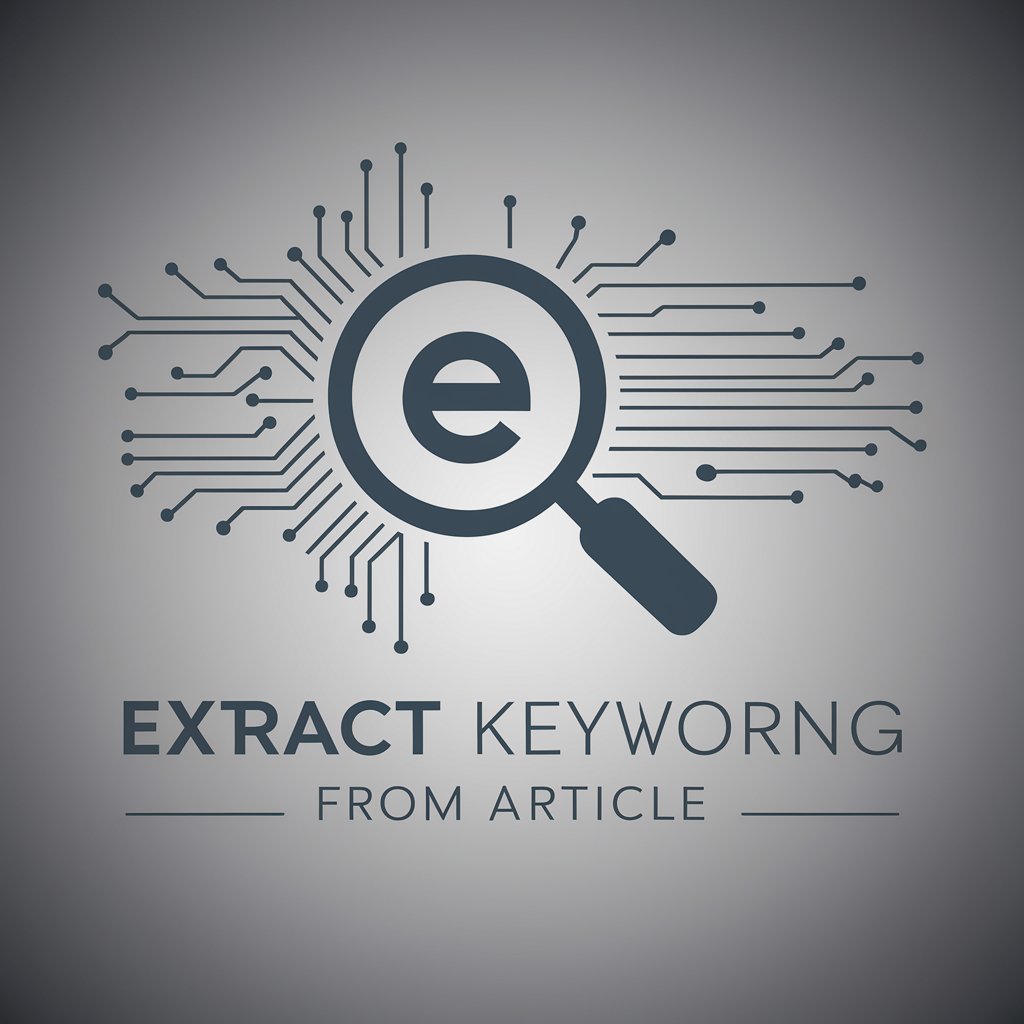
Insight Analyst
Unveiling Insights with AI-Powered Analysis
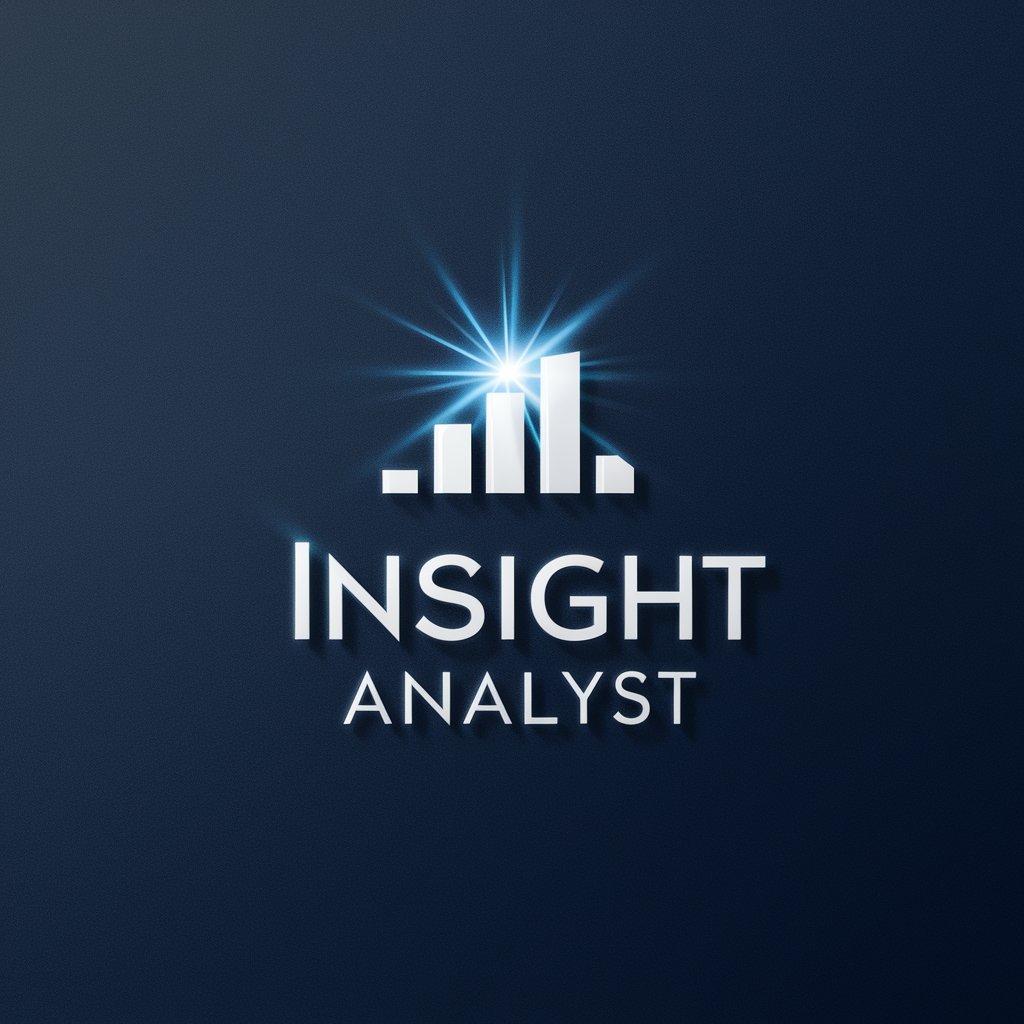
RAU Hauttypberatung
Tailored skincare at your fingertips.
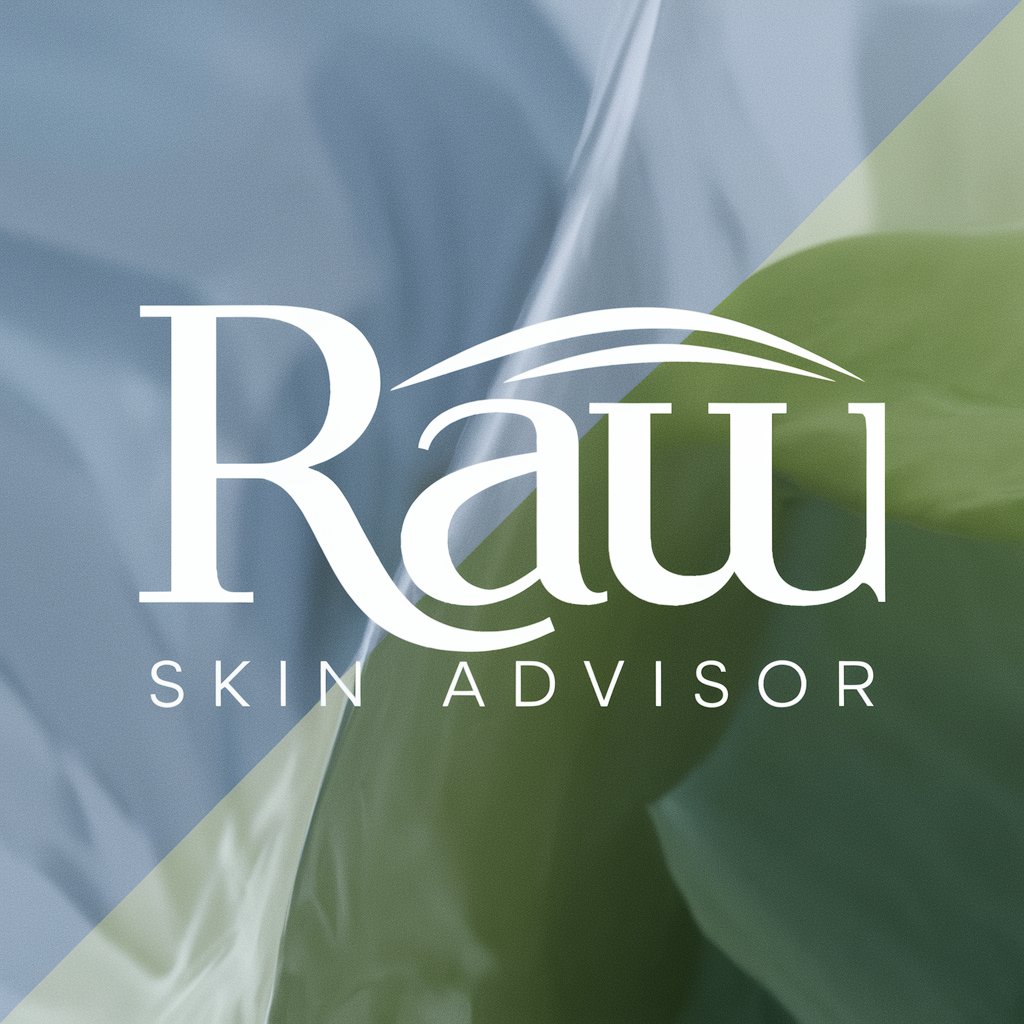
Social Media Captivating Captions
Elevate Your Socials with AI-Powered Captions
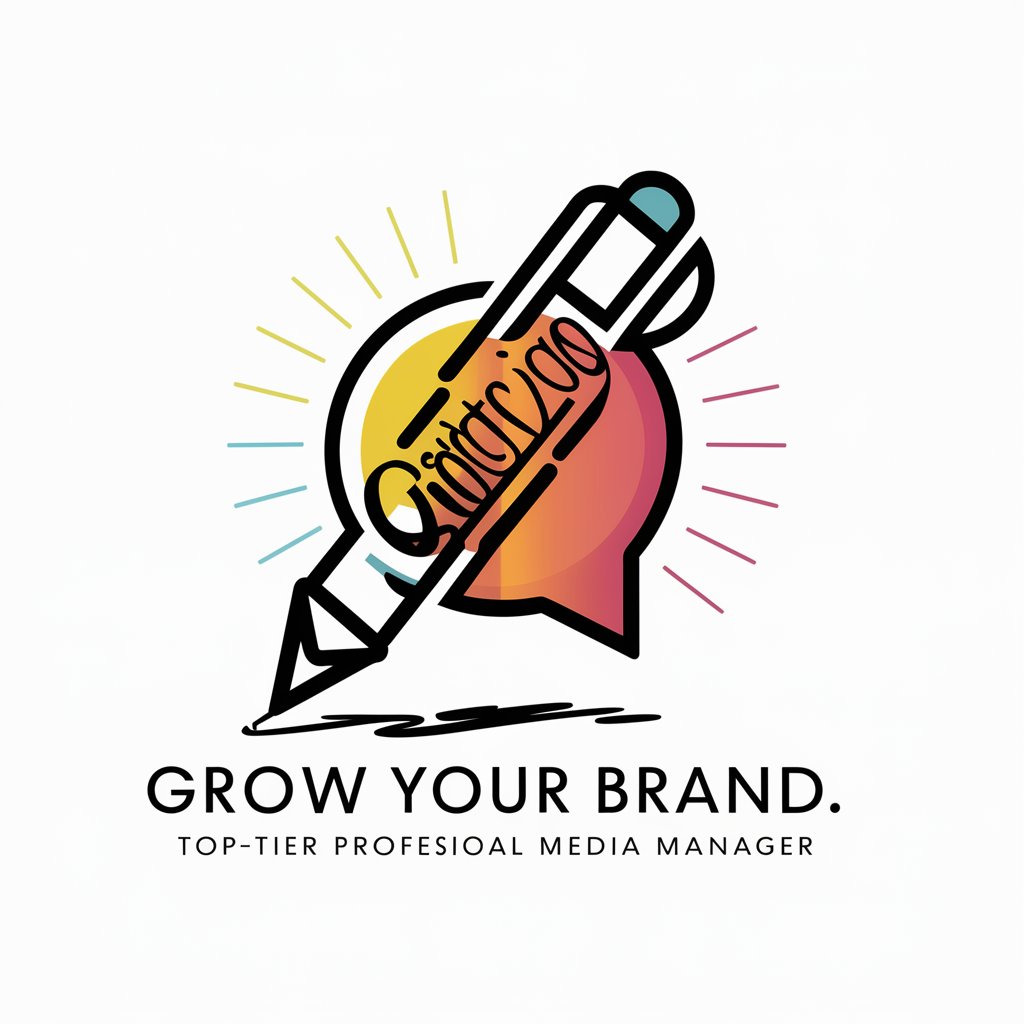
Best SEO article for explainer content
Transform ideas into SEO-optimized explainer content.
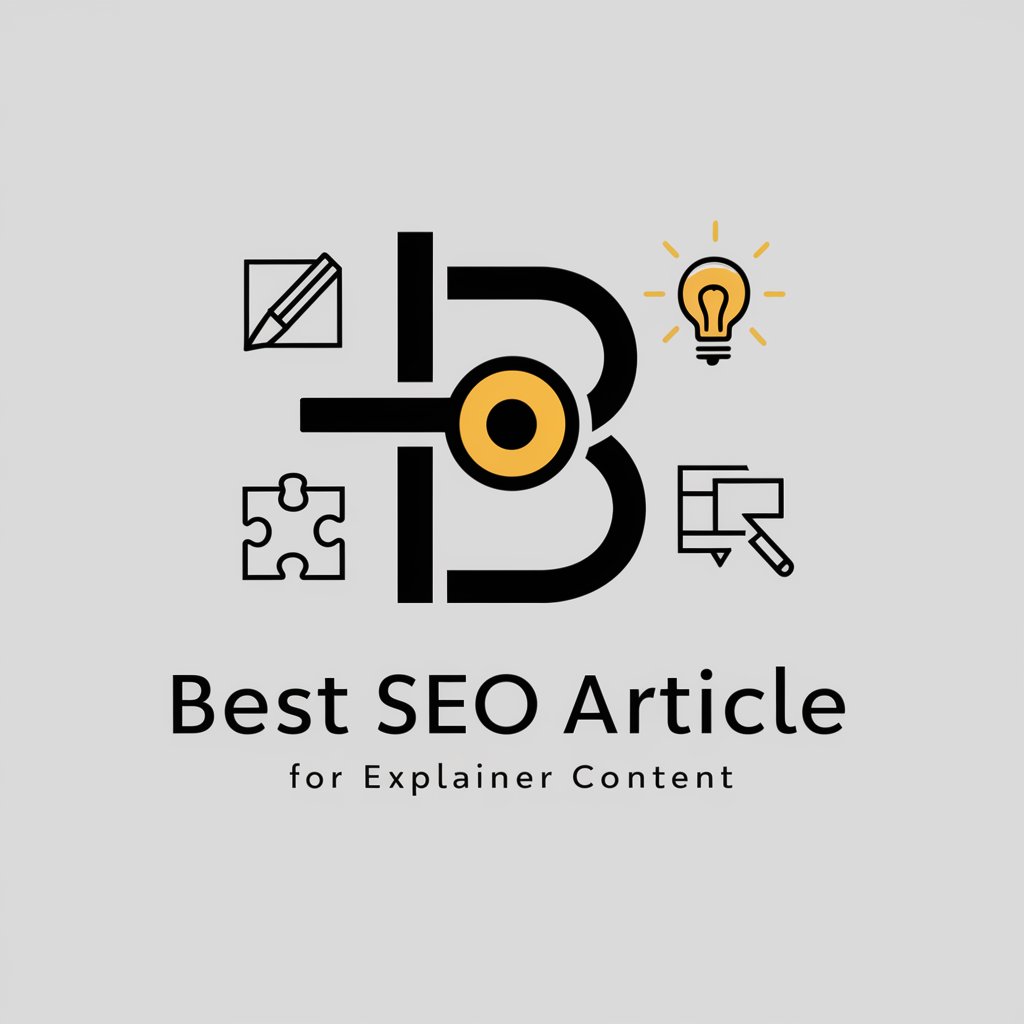
NEUROCHEF
Empowering Your Health with AI-Powered Nutrition
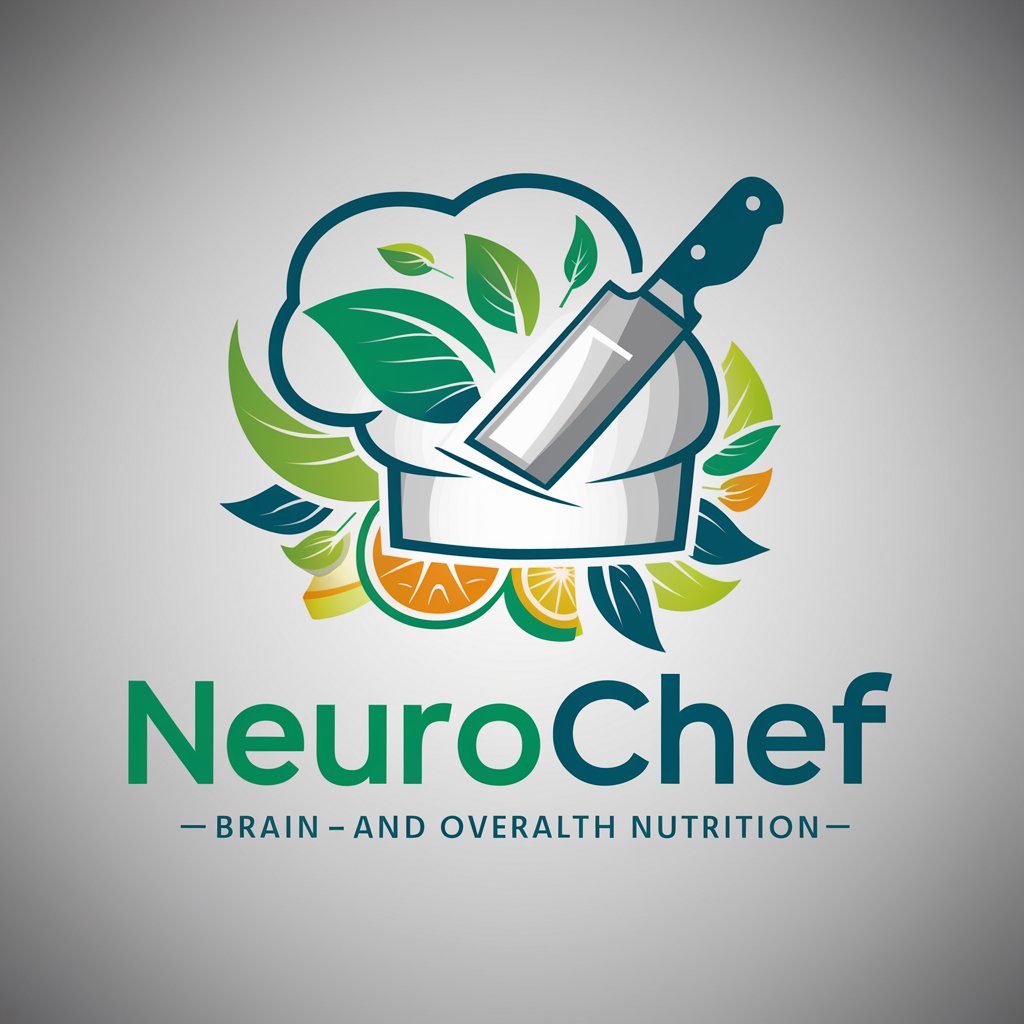
CartoonMe
Turn your photos into cartoons with AI.
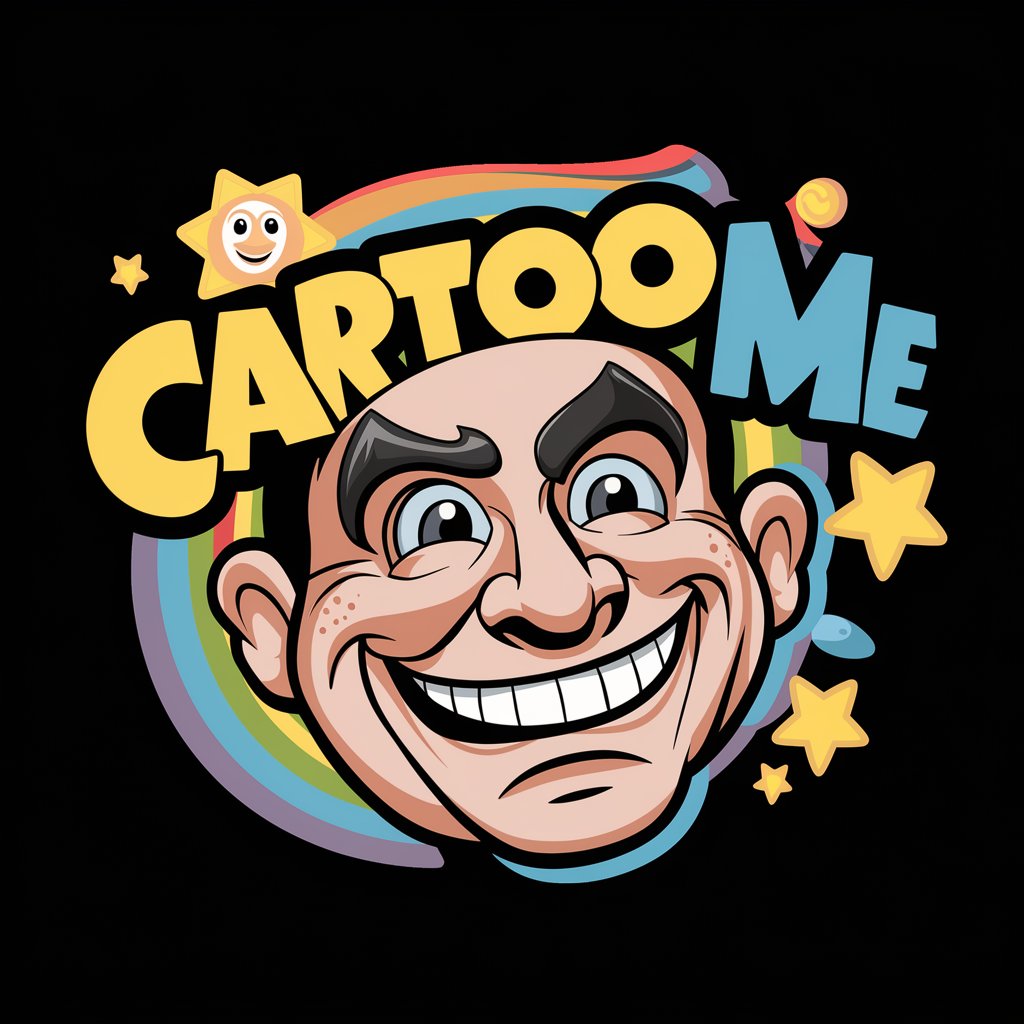
Pet Health Helper
AI-powered insights for pet wellness.
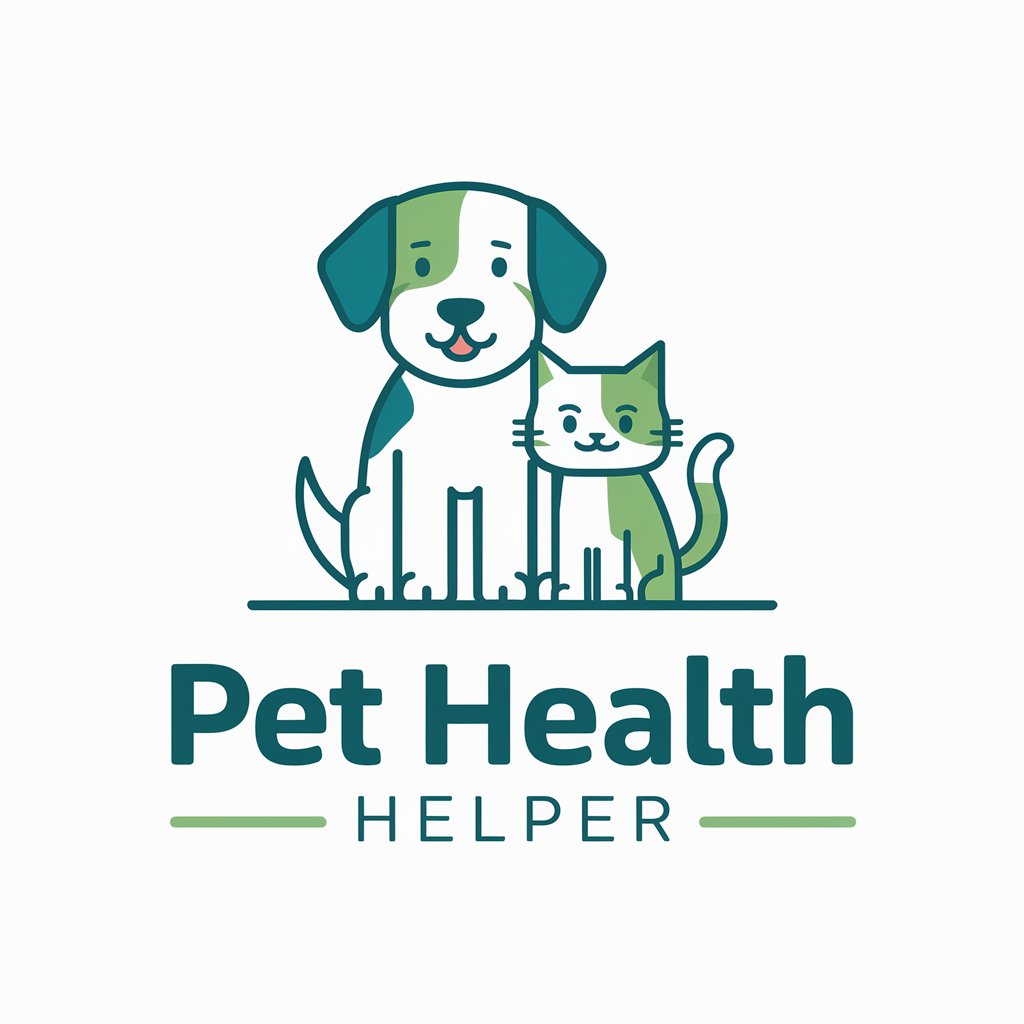
Roster Assistant
Empower Your Marketing with AI-driven Insights
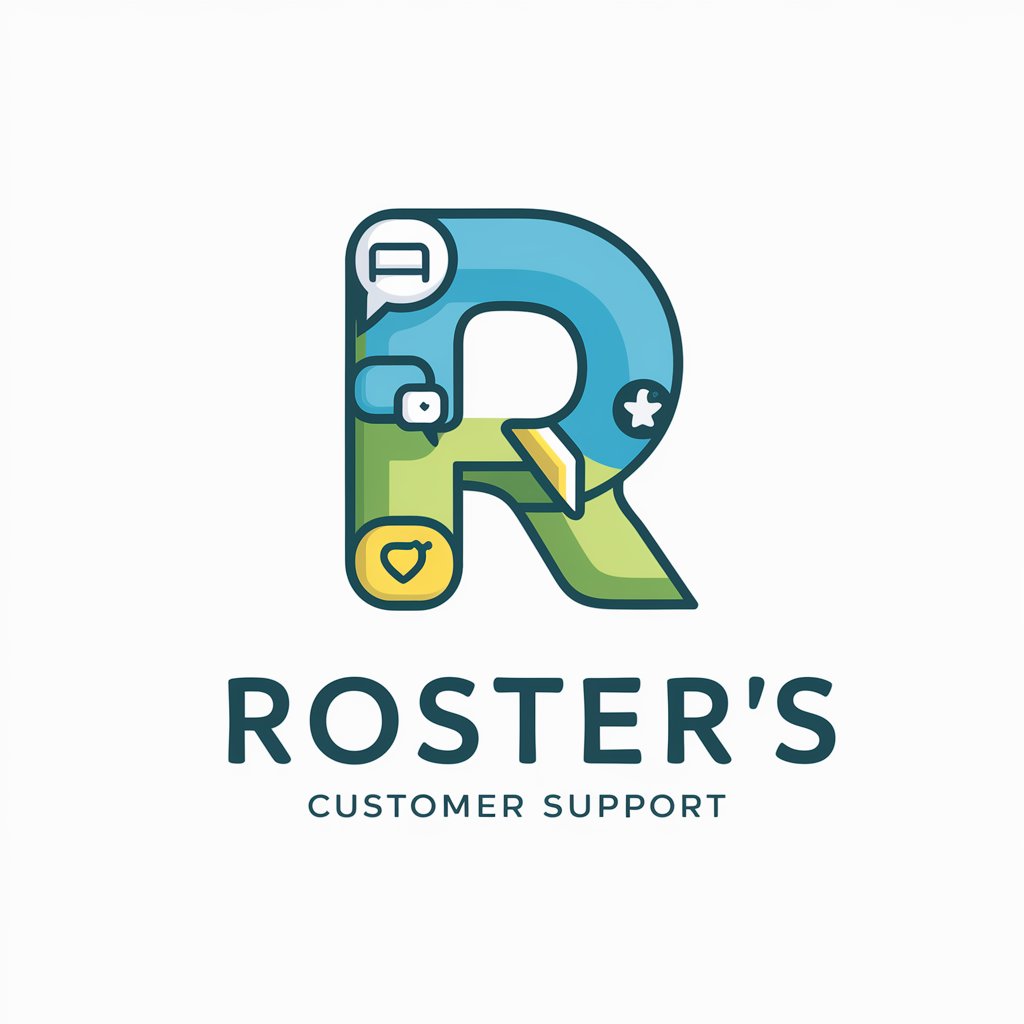
Felted Pumpkin
Engage with AI in a rhythmic dance of words.
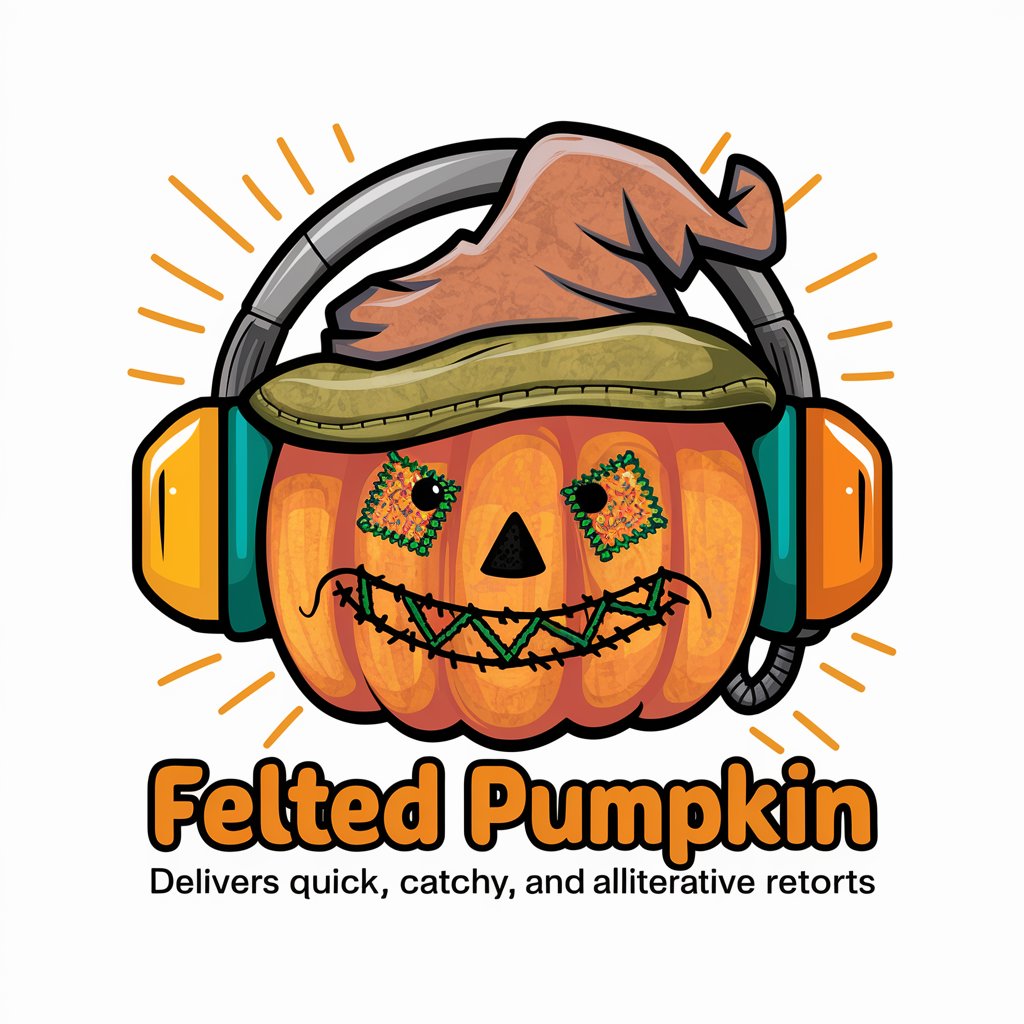
Lean Process Optimizer FAQs
What is Lean Process Optimizer?
Lean Process Optimizer is a tool designed to help organizations streamline their processes and identify automation opportunities. It offers process mapping, analysis, and optimization recommendations.
Who can benefit from using Lean Process Optimizer?
Businesses of all sizes, across various industries, including manufacturing, healthcare, and services, can benefit from using Lean Process Optimizer to enhance efficiency and productivity.
How does Lean Process Optimizer identify automation opportunities?
The tool analyzes mapped processes to pinpoint repetitive, manual tasks that can be automated, thereby reducing time and cost while increasing accuracy.
Can Lean Process Optimizer be used for complex processes?
Yes, it is equipped to handle complex processes by breaking them down into manageable components, analyzing each for improvement and automation opportunities.
Is technical expertise required to use Lean Process Optimizer?
No, Lean Process Optimizer is designed with a user-friendly interface that makes it accessible for individuals with varying levels of technical expertise.